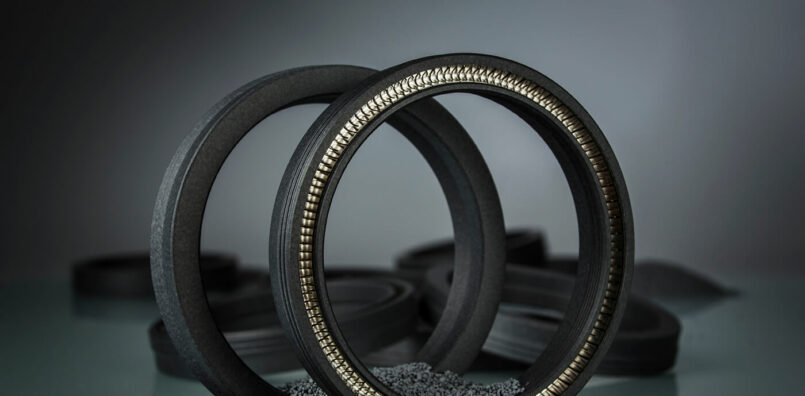
Valves for the process industries perform a critical service in chemical, oil and gas, cryogenic, and marine environments for industrial and technical gases, steams, and liquids. Due to their application, design engineers that manufacture these products must develop solutions for numerous conditions. Included among them are high-temperature, high-pressure, and high-cycling applications.
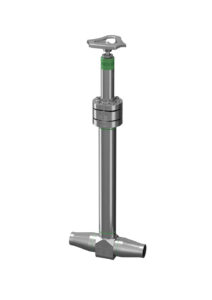
HEROSE FullX-Valve
One of the basic functions of a valve is to control, regulate or direct the flow of media within a system or process. Every valve contains sealing components that are essential for its safe operation. When the seal is designed correctly, end users of industrial applications benefit not only from smooth operation, but also from increased safety, reduced maintenance requirements and durability.
However, as process industry infrastructures age, improvements, and upgrades are inevitable. And this means that operators must take the time to answer two common process improvement questions. First, how to cost-efficiently replace legacy valves with modern, state-of-the-art products that offer as little disruption and downtime as possible? Second, how can the upgraded products and materials meet the industry’s rigorous performance and material quality requirements?
HEROSE GmbH, an international manufacturer of safety valves for the process industries, in collaboration with seal manufacturing experts Dichtelemente Hallite GmbH, found a successful solution to both challenges for their FullX valve. Together, they designed and implemented a customized high-performance sealing system that significantly reduced maintenance efforts for the valves while increasing their service life. As a result, HEROSE was not only able to significantly reduce its costs but also make a valuable contribution to sustainability.
At Dichtelemente Hallite, the development was led by a team that together looks back on more than 65 years of technical experience; nevertheless, success did not happen overnight. While one can replace a single seal in the short term, installing an entirely new sealing system in a series takes much more time. The process involves several steps, starting with a comprehensive consultation and thorough assessment.
Consultation and evaluation
Each customer’s needs are application specific, so the process of finding the right solution must begin with a detailed discussion about the problem. In search of an alternative solution for common but no longer performing and high-maintenance stuffing boxes, HEROSE turned to Dichtelemente Hallite. The sealing manufacturer asked the right questions based on its many years of experience and looked at the customer’s challenges and needs from a holistic perspective.
Throughout the process, tests were carried out and regularly evaluated. In the course of this, Hallite’s experts recommended expanding the single seal into a multi-part sealing system to ensure the desired functionality of the valve while saving needed space.
Regulatory compliant materials
One important aspect is the selection of suitable materials for seals. This is because media such as industrial gases, oxygen and cryogenic liquids require high-performance materials that are designed for extreme environments – materials that can do far more than those used in the past.
In addition, they have to comply with a wide range of regulations and specifications, such as BAM (Bundesanstalt für Materialforschung und -prüfung), FDA, KTW, etc. This also means that manufacturers must work closely with material suppliers to find the right solution for each application because every process is unique, and the possibilities are endless.
From outdated stuffing boxes to state-of-the-art sealing solutions
HEROSE faced several challenges with a sealing system comprised of stuffing boxes. First, the system did not adjust automatically, presenting rough tolerances. These made the valve prone to leakage and required frequent manual adjustment by trained personnel. This made the system high-maintenance and costly.
Confronted with these conditions, Dichtelemente Hallite assessed various design and material combinations. The resulting solution was the OPTISEAL® Multispring, a spring-preloaded PTFE U-Ring, with several independently preloaded sealing lips. Metallic finger springs are positioned within the seal so that each sealing lip is preloaded separately by a spring.
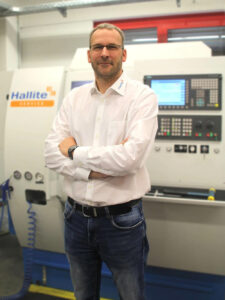
Stephan Estel, Hallite Product group Manager
Extra edges provide an added safeguard against leaks—a key feature suitable for any stem valve seal used in gas or dynamic applications. This design also gives the entire seal a high degree of flexibility, which reduces friction and, thus, premature wear. A modified PTFE with carbon filler was chosen, which is tailored to the applications and has the necessary approvals.
In the course of the tests, Dichtelemente Hallite recommended the use of an additional one-piece wiper/bearing element. The bearing prevents metal-to-metal contact, and the wiper protects the system from contamination.
With the OptiSeal® Multispring, the customer now has a permanent spring pre-tensioning solution that ensures permanent tightness. It is also easy to install, low maintenance, low friction, and highly durable, offering longer service life.
The sealing solution was tested and proven to last three times longer than the incumbent stuffing boxes. Due to its success, HEROSE is using this solution in their FullX valve with plans to convert other valve series to this solution in the future.
Expertise, knowledge, and capabilities
Partnering with seal specialists like Dichtelemente Hallite GmbH offered HEROSE several advantages, with expertise and knowledge topping the list. For example, Lars Johannsen, who has been serving the process industry as a sales engineer for Dichtelemente Hallite for 40 years, has an incomparably deep knowledge that comes from working with a wide variety of companies daily. Lars works with Stephan Estel, Product Group Manager HPP at Dichtelemente Hallite who has over 25 years of experience in the development of sealing solutions for the process industry, and with other colleagues, they found the optimal solution for the customer.
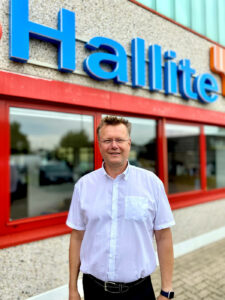
Lars Johannsen, Hallite Sales engineer
When you realise in the development process that standardised solutions do not meet the desired requirements, it is important to have a partner at your side who thinks and acts holistically and application-specifically. Hallite is a company that essentially produces and develops seals and construction parts made of high-quality special polymers. The special thing about them is that they combine their standard programme and their knowledge with the services that they offer in addition to the seals.
Finally, customers benefit from a global network of distributors, suppliers, and trading partners.
Conclusion
Manufacturers of valves for the process industries face shorter delivery times and increased requirements for high-performing, regulatory-compliant materials. Partnerships with experienced seal manufacturers are proving beneficial to achieve these business-critical objectives. By working together, new, innovative products are emerging for greater efficiency, safety, and sustainability.
*The Spring Energized Seals and the OptiSeal® Mutltispring originate from Hallite’s sister company,CDI Energy Products. These products were introduced to HEROSE, modified to address the customer’s issue, and manufactured by Dichtelemente Hallite GmbH.